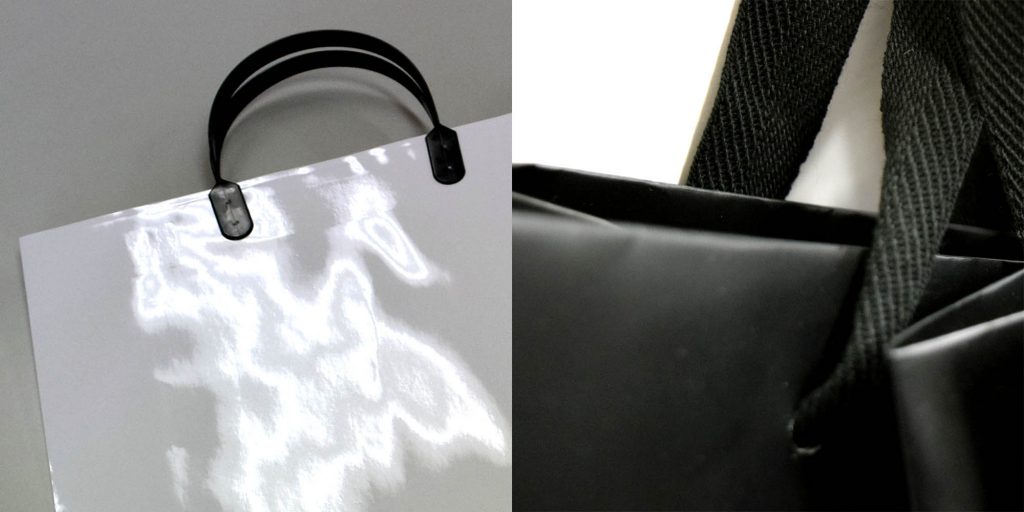
オリジナルで作る紙袋では、外観を変えるような幾つかの加工を施す事が可能です。勿論加工なしでお使い頂く事も可能なのですが、例えば紙袋に光沢や高級感を与えたり、ある程度の防水性能を持たせる事も可能です。また、印刷インキが手や服に色移りすることを防いだりすることもできます。ここではそのような、紙袋に対して付加価値を与えることについて解説してみようと思います。まずはPPフィルムについてです。
PPフィルムとは
PPというのはポリプロピレンの略で、昨今SDGs提唱や海洋性プラスチック問題、レジ袋有料化等でクローズアップされる事の多い、プラスチックの種類の内の一つです。(これらに関しては別ページでも解説していますのでそちらもご覧ください。)プラスチックを分類していくと、ポリエチレンやポリエステル、ペットボトルやPVC等色々な種類のものがあるのですが、そのうち最も一般的に広く使われているものの一つにポリプロピレンがあります。上記の様な環境問題等で昨今ではネガティブなイメージがつきまといますが、プラスチックは扱いやすく、安価な素材である事が利点なので、大量に存在するプラ製品と上手につき合い、コントロールする事により問題の解決に繋がることが最良でしょう。
このポリプロピレンを使ったフィルムを紙袋の表面に貼る事ができます。厚みは20マイクロメートル前後です。この厚みは一般的にはスーパーマーケットで持ち帰りに使われているレジ袋の厚みと同じぐらいで、かなり薄いものです。紙袋に貼った場合、見た目に厚みが増す、というような事はありませんが、紙素材自体に「ハリ」が出ますので、触感的には紙袋がシッカリしたような印象になります。
期待できる効果としては、
- 耐久性の向上
- 印刷の保護
- 外観の変化
- 耐水性
- 紙割れ防止
等があります。
「耐水性」と「紙割れ防止」については名称そのままで、水を弾きやすくなる事と、折り加工を行なった場合の紙割れを防ぎます。その他の特徴を以下で説明致します。
耐久性の向上
これは単純に紙の破れ耐性が向上します。紙袋の場合、特に持ち手部分に関して言えば、紙に穴を開けて持ち手紐を通し、紐の結び目で外れない様にするケースが多いのですが、この部分の強度、延いては紙袋自体の重さに対する耐性が上がります。単純に紙の材質としての強度が上がるので紙袋の様に折り加工が施される部分も破れにくくなります。
印刷の保護
これは2つの意味があり、単純に仕上がり面に印刷されたデザインが接触等により損なわれる事を防ぎ、同時に同じく接触等により例えば衣服、皮膚、その他への印刷インクの色移りを防ぎます。PP貼りを行なっていない紙袋の表面は、例えば雨や汗等の水分でインクが浮くことにより色移りしやすくなり、例えば購入物の持ち帰り時、雨天や汗をかいた際の水分等で色移りがおこり、クレームの原因になったりします。別の記事で紹介する予定の、透明ニスの全面印刷を行なう事により、ある程度の色移りを防ぐ事も可能なのですが、やはりニスでは完全に防ぐ事は難しく、PPフィルムでは確実に色移り問題を解消できます。
外観の変化(光沢の有無)
PPフィルムには主に2種類のフィルムがあり、グロスPP(クリアPP)とマットPPと呼ばれます。これは表面の光沢があるかないかの違いです。コストの観点からは、マットPPのほうが少しだけ高いです。こちらの弊社製作実績サイトでも実績をご覧いただけます(グロスPP、マットPP)。
グロスPP(クリアPP)
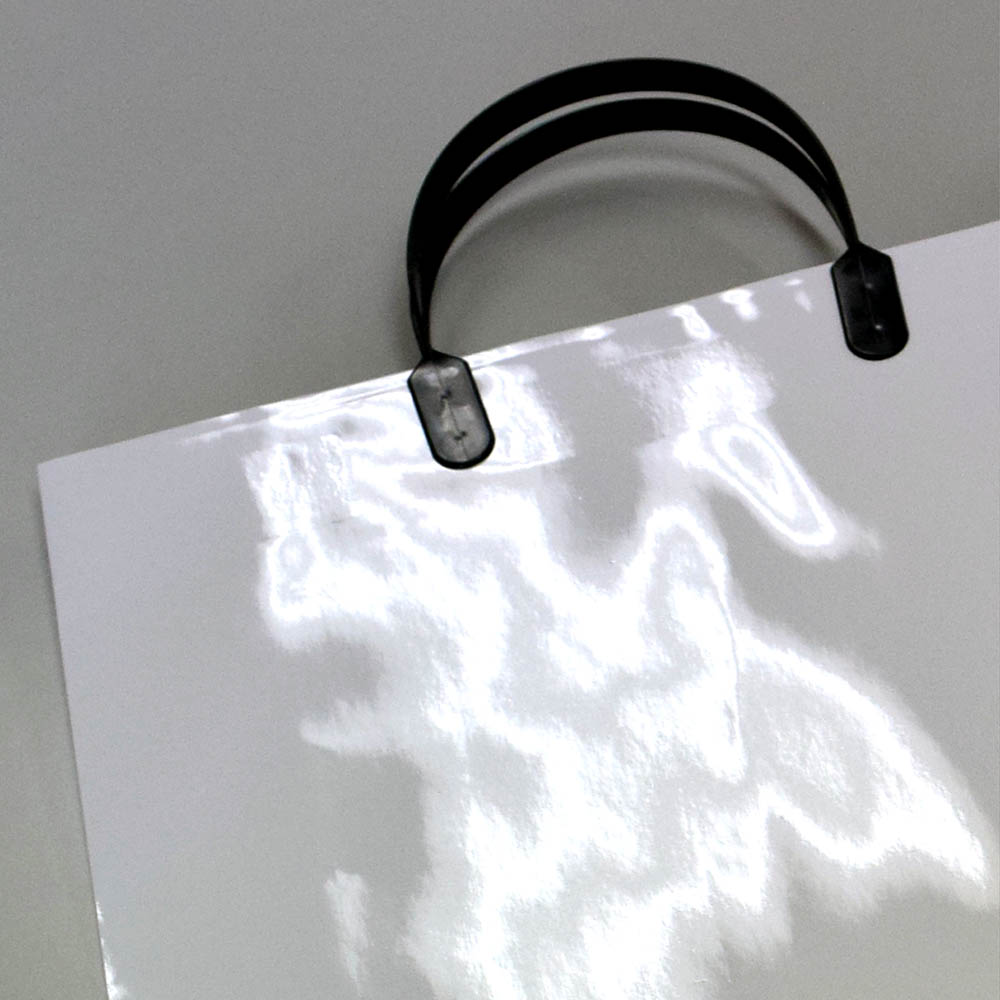
滑らかな光沢を紙袋に与える事ができ、外観の印象が大きく変わります。ある程度の高級感と、触った感じでもその特徴を感じる事ができます。光沢面は鏡面とまではいきませんが豊かな光沢で、印刷内容を鮮やかに際立たせる効果があります。
光沢を与えるだけでなく、紙への印刷に対する色調等にも影響を与えます。具体的には、写真やイラストの色の濃度が上がる様に見えます。オフセット印刷等は拡大してよく見ると小さい網点で表現されている事が分かりますが、この網点がPPフィルムを貼る際の圧力で僅かながら膨張し、色が濃くなる一因となるというものです。また、薄いながらも透明の膜を貼っているので、光の屈折等で見え方が変わるという事もあります。主に変わり安い色は赤で、主にこの現象は「赤浮き」と呼ばれます。これは製法上防ぐ事が難しい一方で、熟練の印刷オペレーターであればある程度変化の度合いを予測し、若干赤を薄めに印刷する、等の方法で対処します。
マットPP
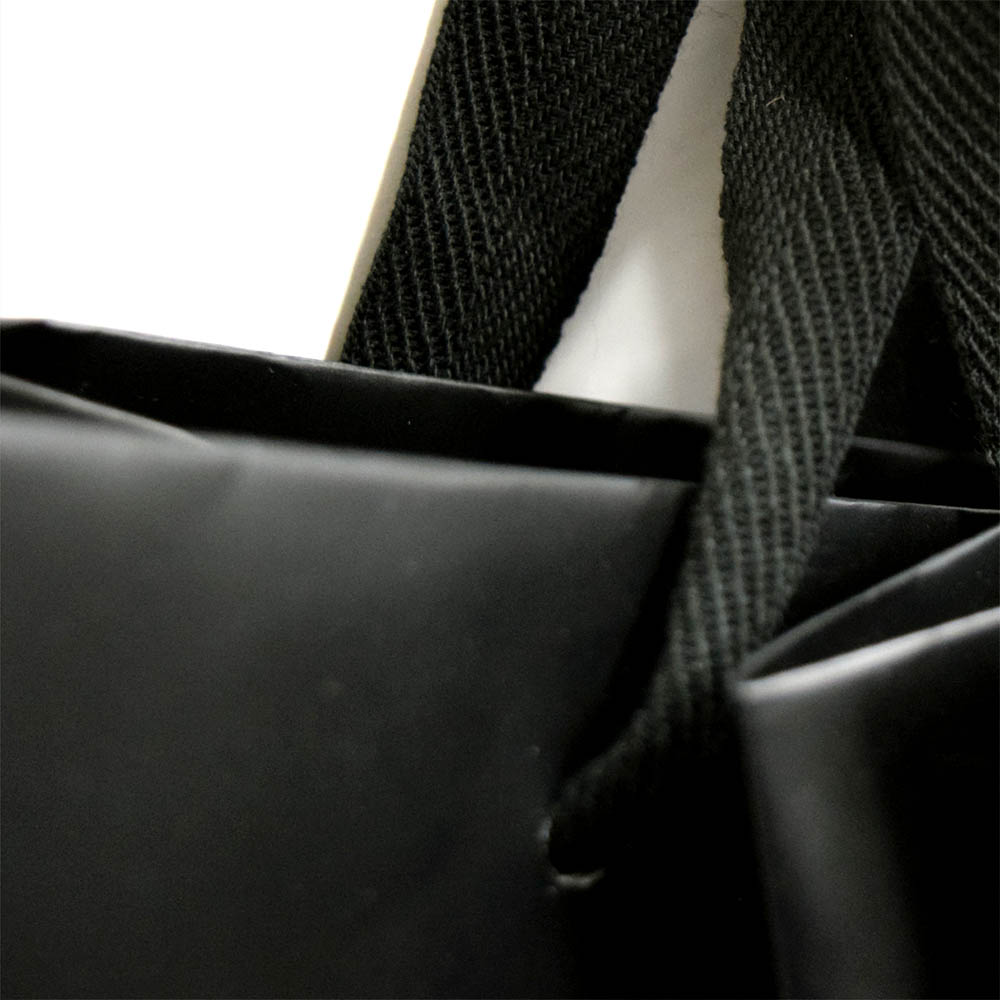
グロスPPと異なり、表面に艶消しのPPを貼る事により、グロスPPよりは落ち着いた印象で、上品でシックな高級感を与えます。こちらも同様に見た目の高級感と同時に、さらっとしたシルクの様な手触りでも高級感を感じる事ができます。
グロスPPと同様に加工を施すと、下地の印刷色調に変化を与えます。グロスPPの場合は濃くなったり、赤くなったりという事が多いのですが、マットPPの場合は印刷が若干暗く沈む、といった傾向があります。発色の良いデザインの場合は注意が必要です。こちらもある程度、印刷の際にやや明るめの仕上げにする等で色の変化を予想する必要があります。
マットPP加工の際に注意しなければならない点はもう一つあり、加工後の表面に傷がつきやすい、といった事が挙げられます。マットPP加工の後に、例えば手作業による折り加工、内職作業等が入る場合、勿論極力気をつけて作業をするのですが、それでも若干の傷が入ってしまう事があります。
本機校正で事前に確認
上記の様に、PP加工を行なう際の色の変化予測がやや難しい事を説明しましたが、量産に入る前に「本機校正」等である程度仕上がりの目星をつけておく事もできます。これは、製品になる時の用紙と、実際のインキ、実際のオフセット印刷機を使ってテストを行ない、本番と同様に印刷・加工を行なって事前にお客様に確認を頂いた上で量産に入る、というものです。この場合、実際に使う紙とインクと機械での作業となるのである程度製品に近い状態のもので事前確認頂ける、というメリットがあります。特に特色での印刷の場合は本機校正と量産で同じインクを使うことになるので、ある程度正確な事前確認が出来る事が大きいです。反対にデメリットとしては、コストが掛かってしまう事が挙げられます。これは印刷代だけでも1色1万前後となってしまう事に加え、実際の用紙も別途購入が必要なためにコスト問題で行なわないケースが殆どです。また、実際に行なったとしても当日の温度、湿度等の条件で微妙に色調が変わったり、乾燥後の色の変化までは予測が難しい、といったような諸々の不確定要素が多い事も問題になります。
その他の生じうる問題
PPフィルム関係ではその他にも幾つか発生する問題があります。
フィルムや印刷インキの温度耐性オーバー
PPフィルム加工を行なう場合はフィルムに塗布されている糊を高温で溶かし、紙へ圧着していく行程が主なのですが、この際の高温が原因で印刷インキの色調が稀に変化する場合があります。これを防ぐには、高温をそれほど必要としない糊をフィルムに塗布し、温度を出来るだけ上げずにフィルム加工を行なう方法で対処できます。ややコストが高くなるのですが、変化のしやすいインキを使う場合は事前にこういったフィルムを用意しても良いでしょう。
パウダー噴射による接着不良等
PP加工の前段階であるオフセット印刷において、例えば全面がベタ印刷、更にはベタの2度重ね印刷等を行なうケースは紙袋では結構あります。この場合、オフセット印刷機から印刷直後に排出される刷り上がりは、非常に乾きにくい状態となっている為、乾燥を促進させるパウダーの量をより多く噴射する必要がでてきます。このパウダーの噴射量が多すぎると、次行程であるPPフィルム加工の際、パウダーの影響で接着がうまくいかず、間に空気が入ったりする問題が起きやすくなります。これを防ぐには、パウダーの種類を変更する、または減らす等で対処します。
最後に
上記の様にPPフィルムを詳しく説明してきました。利点の多いPPフィルム加工は幾つか難しい部分もあり、ある程度の予測と経験値が必要な場面もあります。弊社では数々の製作事例があり、問題に対処してきた実績もありますので、紙袋の加工をお考えの場合は是非お気軽にご相談頂ければと思います。